Balancing Safety and Efficiency: New Regulations regarding Autonomous mobiles robots.
- Paula González
- Sep 19, 2023
- 3 min read
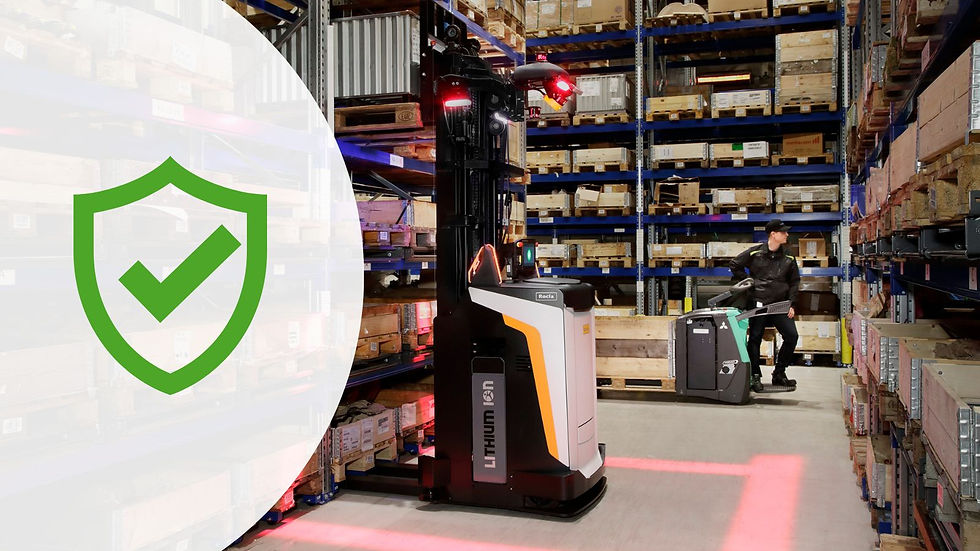
The swift advancement of automation within the industry, especially in the utilization of Automated Guided Vehicles (AGVs) and Autonomous Mobile Robots (AMRs) in both production and warehouse settings, has compelled the revision of international regulations governing their usage to guarantee the safety of both machinery and individuals.
There's no doubt that robotics brings significant benefits to process optimization and productivity. However, the proliferation of automated devices and autonomous vehicles in shared spaces with humans increases the risks of accidents.
ISO 3691-4 Standard and Pilz's Educational Resources for Autonomous Vehicles:
Until 2020, the specific standard in force in Europe was EN 1525:1997, which, with its 23-year age, had become obsolete as it couldn't anticipate the pace at which technology would develop.
The publication of ISO 3691-4 in 2020 updated the primary international standard, providing both manufacturers and operators with a robust reference guide.
However, this new standard is much more complex than its predecessor. It outlines various parameters and concepts to consider during the design of an industrial mobile platform system. The text expands on safety function requirements for AGVs and defines the means to validate their automated functions. Additionally, it sets performance levels required for vehicle supervision functions, different operating modes, and brake control.
According to legal frameworks, each manufacturer is responsible for implementing preventive measures to ensure the safe coexistence of mobile platforms and humans. Each AGV or AMR must incorporate the necessary technology to prevent collisions and other types of accidents.
The issue is that there are increasingly more autonomous vehicles operating in spaces where, not long ago, only humans worked. This compels companies to approach safety from a global perspective, adhering to regulatory requirements and seeking appropriate solutions, both legally and in terms of productivity.
The obvious conclusion is that it's most practical to seek an expert partner in safe automation, such as Pilz, which has developed a comprehensive package of services for implementing secure AGV or AMR applications, from the design phase to commissioning, including an extensive program of specific courses.
The Pilz Method for Safe Mobile Robotics Integration
The Pilz method is structured into nine steps, taking into account the following aspects:
Legal environment and applicable standards (Machinery Directive, ISO 12100, and ISO 3691-4 for the European Union).
Safety requirements: potential hazards and applicable methods for risk reduction.
Safety functions: considering functional safety requirements of the vehicle and its interaction with other machines.
System verification: ensuring the proper implementation and operation of safety measures, detection systems, stop times, stability, and other critical system elements.
User information: instruction manual and additional safety measures, such as visual and auditory signals warning of the AGV's approach.
Integration space characteristics: detailed knowledge of where the autonomous vehicles will operate.
Application area assessment: considering specific task-related factors, such as load transfer.
Other factors to consider: if additional machine equipment, such as lifts, turning stations, or closures, will be involved.
Personnel training: training individuals operating AGVs and those working in the same workspace to understand existing risks and how to avoid them.
Specific Course for the Safe Use of Automated Guided Vehicles:
Regarding training offerings, Pilz has developed the "Safe Use of Automated Guided Vehicles and Systems" course, aimed at manufacturers, integrators, and users with special responsibilities related to AGV use. The content is divided into three parts: legal framework, Automated Guided Vehicle (AGV), and a combination of automated guiding systems, covering all significant aspects of mobile platform use in the industrial environment. Some benefits of this specific training include:
Learning the correct application and implementation of relevant regulations and directives, as well as proven technical procedures for AGV integration.
The ability to manage the risk associated with the installation and use of AGVs in the production facility.
Competitive advantages in using automated guiding systems by applying the most suitable safety technologies.
The knowledge required to assess and evaluate existing facilities in terms of automated guiding system safety.
Comments